Metallurgical Abstracts on Light Metals and Alloys vol.54
Formation of a phosphoric acid compound film on an AZ31 magnesium alloy surface using cavitation bubbles
Masataka Ijiri*, Koji Yamaguchia**, Shoichi Kikuchi***, Fumihiro Kato****, Yui Kunieda****,
Hiroki Sakurai****, Takayuki Ogi**** and Toshihiko Yoshimura****
*Tokyo Metropolitan University, 1-1 Minami-Osawa, Hachioji, Tokyo 192-0397, Japan
**Tokyo Denki University, 5 Senju-Asahi-Cho, Adachi-Ku, Tokyo 120-8551, Japan
***Shizuoka University, 3-5-1 Johoku, Naka-ku, Hamamatsu-shi, Shizuoka 432-8561, Japan
****Department of Mechanical Engineering, Sanyo-Onoda City University
[Published in Surfaces and Interfaces, Vol. 25 (2021), 101194]
https://www.sciencedirect.com/science/article/abs/pii/S2468023021002716?via%3Dihub
E-mail: ijiri[at]tmu.ac.jp
Multifunction cavitation, Residual stress, Hardness, Water jet peening, Mg alloy
Cavitation processing with chemicals was used to improve the corrosion resistance of an AZ31 magnesium alloy surface. This technique improves corrosion resistance by the formation of a phosphoric acid compound film on the surface of the Mg alloy. However, the processing conditions affect the state of the film; therefore, the effect of the distance from the nozzle to the specimen surface (stand-off distance) on the cavitation state was investigated. This technique employs phosphoric acid and water for processing; therefore, immersion tests were performed with various aqueous concentrations of phosphoric acid to evaluate corrosion resistance. Cavitation processing employs water jet peening (WJP) and multifunction cavitation (MFC). The stand-off distance at which the phosphoric acid-based film was easily formed on the Mg alloy surface was specified for each processing condition. In addition to the formation of a phosphoric acid compound film, the hardness and compressive residual stress at the surface were improved after each process. A film was formed on the surface during the immersion test; however, the thickness of the film was negligible. These results confirmed that cavitation processing is effective for the formation of a phosphoric acid compound film on Mg alloy surfaces.
Figure 1 shows the surface hardness after each process with different stand-off distances. The hardness of the unprocessed specimen surface was 64.3±3.4 HV. The hardness of the surfaces processed by MFC and WJP, which did not involve chemicals, increased with respect to the unprocessed specimen surface. The stand-off distances with the highest surface hardness were 65 mm for MFC and 45 mm for WJP. In addition, although there was no significant change for each stand-off distance when processing with chemicals, the surface hardness gradually decreased as the stand-off distance increased. It is considered that this change in surface hardness was due to the film formed on the surface by processing using chemicals, as it will be discussed later.
Figure 2 shows the residual stresses after each process with different stand-off distances. The residual stress for the unprocessed specimen was -63 MPa. The residual compressive stress at the surface increased after each process with different stand-off distances, but was largely unaffected by changes in the stand-off distance. The residual compressive stress at the surface for each stand-off distance was -110 MPa after MC-MFC and -102 MPa after MC-WJP. This residual compressive stress was not significantly affected by the change in the stand-off distance; therefore, the average value of the residual stress for each stand-off distance is shown. In this measurement, the stress was measured for the surface on which the film was formed. In this stress measurement, the film may interfere with X-rays, so each process was performed using only tap water. The residual stress at the surface after each process increased the residual compressive stress, but the change was not significantly affected by the stand-off distance. For the residual compressive stress, the residual stress values at each stand-off distance were averaged in the same way as for the surface processed with chemicals. The value for the surface after WJP was -109 MPa, and that for the surface after MFC was -115 MPa. The use of chemicals or water did not change the value of residual compressive stress.
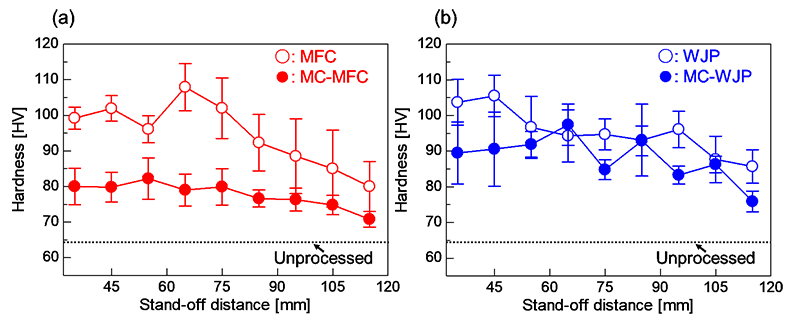
Fig. 1 Surface hardness after (a) MFC and (b) WJP processing with various stand-off distances.
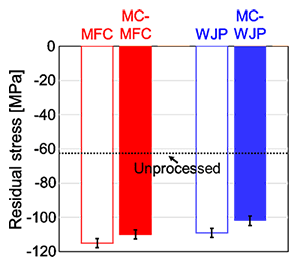
Fig. 2 SEM images of specimen surfaces after treatment for 2 min: (a) MC-WJP and (b) MC-MFC. Panels (a) and (b) are enlargements of the outlined regions in Figs. 2(b) and 2(c), respectively.