Metallurgical Abstracts on Light Metals and Alloys vol.54
Change in microstructure and crystal orientation of an A5052 aluminum alloy processed by multi-directional forging at room temperature
Keizo Kashihara* and Arata Nakatsuji**
*Department of Intelligent Mechanical Engineering, Wakayama National College of Technology
**Student, Department of Intelligent Mechanical Engineering, Wakayama National College of Technology
[Published in Journal of The Japan Institute of Light Metals, Vol. 70 (2020), pp. 459–466]
https://www.jstage.jst.go.jp/article/jilm/70/10/70_701002/_article/-char/en
E-mail: kashihara[at]wakayama-nct.ac.jp
Key Words:multi-directional forging, aluminum alloy, texture, sever plastic deformation, ultra-fine grain
A commercial A5052 aluminum alloy was processed by multi-directional forging (MDF) to 6 passes in a total strain of 4.8 at room temperature. Microstructures and crystal orientations were examined by the electron back-scatter diffraction method. The change in crystal orientations was discussed from two models, the minimum work (Taylor) and the maximum resolved shear stress (Sachs). Ultra-fine grain structure below 1m was developed in the specimen after the MDF for 6 passes. The analysis using crystal orientation index of {hkl} <uvw> indicated that the main components of texture after MDF for 6 passes were {011} <100> and {011} <110>, which were parallel to the compression plane in the final pass of MDF and the compression axis before two passes, respectively, in the specimen coordinate system. Regardless of the number of MDF pass, the main component was {011} <100>. The plastic deformation in MDF from 1 to 3 passes was mainly explained by the Sachs model, however this model could not apply to the formation of the texture after MDF for 6 passes.
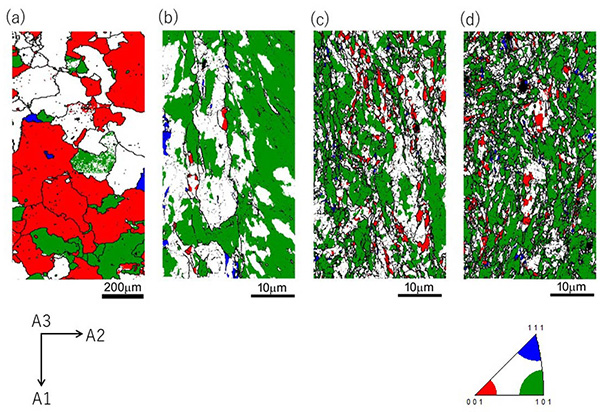
Crystal direction maps in (a) the start material specimen and the specimens after MDF for (b) 1pass, (c) 3 passes, and (d) 6 passes. The directions were parallel to the final compression axes.