Metallurgical Abstracts on Light Metals and Alloys vol.56
Design of Titanium Alloys Insensitive to Thermal History for Additive Manufacturing
Masato Ueda*, **, Chang Ting Hsuan***, Masahiko Ikeda**** and Takayoshi Nakano*****
*Faculty of Chemistry, Materials and Bioengineering, Kansai University
**Carbon Neutrality Research Centre, Kansai University
***Graduate School of Science and Engineering, Kansai University
****Nihon Superior Co., Ltd.
*****Division of Materials and Manufacturing Science, Graduate School of Engineering, Osaka University
[Published in Crystals, Vol. 13 (2023), pp.568–579]
https://doi.org/10.3390/cryst13040568
E-mail: m-ueda[at]kansai-u.ac.jp
Key Words: titanium; zirconium; 3D printing; laser scanning; electrical resistivity
Powder bed fusion is the most common technology used for 3D printing, where thermal energy is used to selectively melt/sinter granular materials into solid shapes. The build platform is then lowered, more powder is added, and the process is repeated for the next layer to fully print the design. As a result, the built-up part is repeatedly heated. Therefore, materials that are not sensitive to thermal history are preferred for this process. The Ti-Zr system forms a continuous solid solution for both β- and α-phases. The presence of Fe in Ti alloys is inevitable; however, it pro-vides some beneficial effects. The purpose of this work was to prepare Ti-Zr-Fe alloys and investigate their heat treatment behaviour. Ti-xmass%Zr-1mass%Fe alloys (x = 0, 5, 10) were prepared with arc melting. The formation of a solid solution of Zr in Ti was confirmed on the basis of X-ray diffraction peak shifts and hardening effects. A small amount of β-phase precipitation was suggested by the change in electrical resistivity after isothermal ageing at 673 and 773 K. How-ever, no obvious phase or microstructural changes were observed. The laser scanning increased the volume of the precipitates and also coarsened them, but the effect was limited.
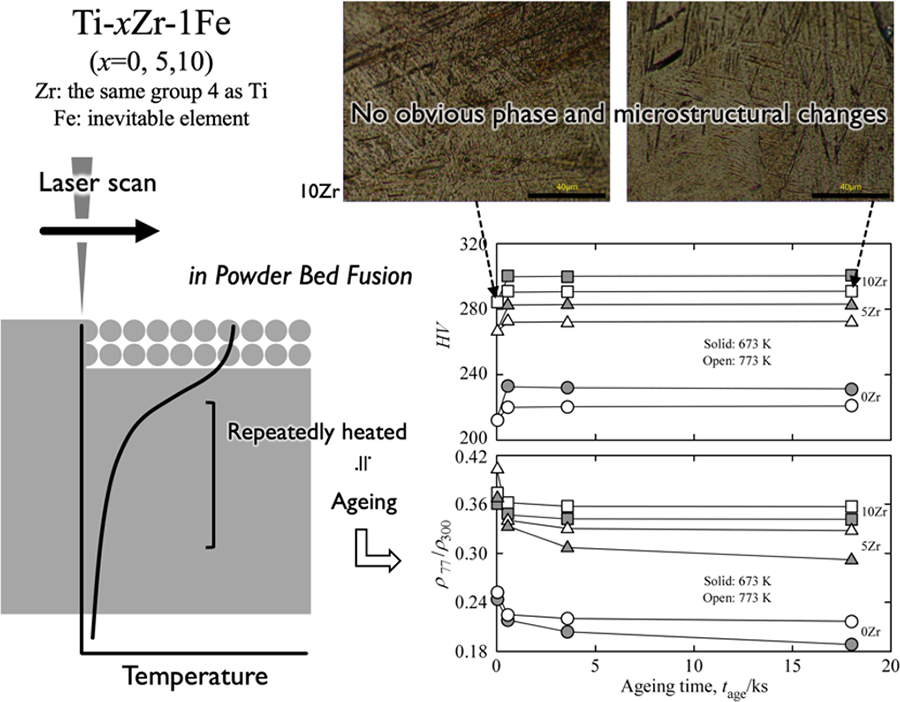