Metallurgical Abstracts on Light Metals and Alloys vol.56
Impact Joining of Pure Copper C1100 and Aluminum Alloy A6061-T6 Plates at Edges
Minoru Yamashita*, Toru Iwatsuka**, Haruchika Taguchi** and Makoto Nikawa*
* Department of Mechanical Engineering, Gifu University
**Graduate student, Gifu University
[Published in Metals, Vo. 12(10) (2022), 1565]
https://doi.org/10.3390/met12101565
E-mail: yamashita.minoru.b8[at]f.gifu-u.ac.jp
Key Words: dissimilar joining; impact process; aluminum alloy; copper; joint efficiency
Joining of pure copper C1100 and aluminum alloy A6061-T6 plates of 5 mm thickness was investigated. The method was developed by one of the authors, in which the newly created surfaces of a pair of plates obtained by high-speed shear were immediately in contact with a sliding motion with a small overlap length. The total processing time was just about a few milliseconds. To create the new surface, high-speed shaving was also tested. The joining was not possible for the full thickness of the plates. A sharp notch was observed at the joint boundary due to a large shear droop in the copper. Shaving decreased the shear droop, and the joint length through the plate thickness became longer. The joining performance was evaluated by a uniaxial tensile test. The joint efficiency reached 100% using the specimen cut out from the really joined boundary. The affected zone of joining was confirmed by the hardness distribution near the boundary. It was about 30% of the thickness of the plate, which was much smaller than that in welding by heat, and no softened zone was found in both materials.
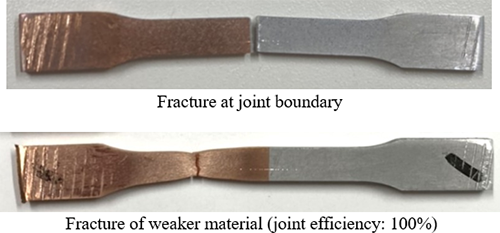
Figure Examples of fracture appearance of joined specimen using shaved surface (left: copper, right: aluminum alloy A6061).