Metallurgical Abstracts on Light Metals and Alloys vol.56
Effect of roller axial position and thickness on a twisted angle in the twist rolling of aluminum alloy 1050 sheet metal
Avanish Kumar1, Shohei Kajikawa1, Takahiro Makiyama2 and Takashi Kuboki1
1 Department of Mechanical and Intelligent Systems Engineering, The University of Electro-Communications
2 Department of Information Science and Mechatronics Engineering, Institute of Technologists
[Published in Metals 2023, Vol. 13 (2023), Issue 2, 383]
https://www.mdpi.com/2075-4701/13/2/383
E-mail: kuboki[at]mce.uec.ac.jp
Key Words: Taper roller; twisting; rolling; skew angle; sheet metal
This paper proposes a new rolling method called "twist rolling" that can continuously form a twisted shape by using taper rollers. The twisted shape of metal sheets is widely used in industrial products such as turbine blades and propellers. Such a shape is normally formed by casting or machining, but there are problems with low efficiency regarding the productivity and yield ratio. Forging processes have also been proposed, but they have problems with the surface property. The present study focuses on rolling to efficiently form a continuously twisted shape. The effect of the axial position of the taper rollers and skew angle on the average specific twisted angle were investigated by experiments and finite element analysis. The relationship between the thickness of sheet metal and the average specific twisted angle was also investigated. The average specific twisted angle decreased as the axial position increased. When the skew angle was smaller and the sheet metal thicker, the average specific twisted angle increased more. Twist rolling can form various twist angles by changing such parameters.
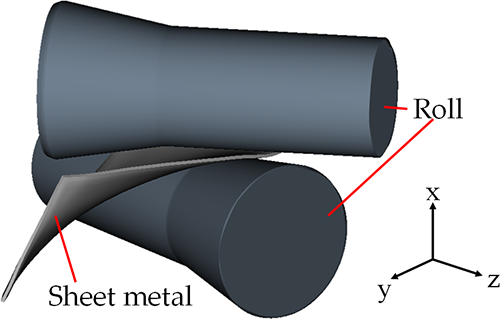
Appearance of sheet metal and FEA model.