Metallurgical Abstracts on Light Metals and Alloys vol.56
Microstructure Evolution and High-Temperature Mechanical Properties of Ti-6Al-4Nb-4Zr Fabricated by Selective Laser Melting
Tomoki Kuroda1, 2, Haruki Masuyama1, 2, Yoshiaki Toda2, Tetsuya Matsunaga2, Tsutomu Ito3,
Makoto Watanabe2, Ryosuke Ozasa4, Takuya Ishimoto4, 5, Takayoshi Nakano4, Masayuki Shimojo1 and Yoko Yamabe-Mitarai6
1 Material Science and Engineering, College of Engineering, Shibaura Institute of Technology, Toyosu 3-7-5, Koto, Tokyo, 135-8548, Japan
2 Research Center for Structural Materials, National Institute for Materials Science, Sengen 1-2-1, Tsukuba, Iabaraki, 305-0047, Japan
3 Department of Mechanical systems Engineering, Faculty of Engineering, Toyama Prefectural University, Kurokawa 5180, Imizu, Toyama, 939-0398, Japan
4 Division of Materials and Manufacturing Science, Graduate School of Engineering, Osaka University, 2-1, Yamada-Oka, Suita, Osaka 565-0871, Japan
5 University of Toyama, Gohuku 3190, Toyama, Toyama, 930-8555, Japan
6 Department of Advanced Materials Science, Graduate School of Frontier Sciences, The University of Tokyo, Kashiwanoha, 277-8561
[Published in Mater. Trans., Vol. 64, No. 1 (2023), pp.95-103]
https://doi.org/10.2320/matertrans.MT-MLA2022021
E-mail: Mitarai.yoko[at]edu.k.u-tokyo.ac.jp
Key Words: selective laser melting, heat-resistant Ti alloys, compression strength, creep
Ti-6Al-4Nb-4Zr (wt%) was prepared by selective laser melting (SLM) under various conditions, and the microstructure evolution resulting from SLM processing and subsequent heat treatments was investigated. The effects of the unique SLM-induced microstructure on the high-temperature compressive strength and creep properties of the samples were then elucidated. Under rapid cooling conditions, the martensitic structure formed in a scale-like pattern, with a 100 mm in size, consistent with the laser scanning pattern. By contrast, under slow cooling conditions, the α/β lamellar structure formed in β grains with a 300 mm grain size instead of in a scale-like pattern. The martensitic structure drastically changed to a Widmanstätten structure during heat treatment. The equiaxed a phase also formed at the interface of the scale-like patterns. By contrast, the α/β lamellar structure did not exhibit a change in response to heat treatment. The compressive strength of the SLM samples was governed by the martensite a size and the grain size, both of which depended on the cooling rate. The dominant creep deformation mechanism at 600 ℃ and under a loading stress of 137 MPa was grain boundary sliding. The creep life depended on the grain size. The HIP treatment improved the creep life because it eliminated pores introduced by the SLM process.
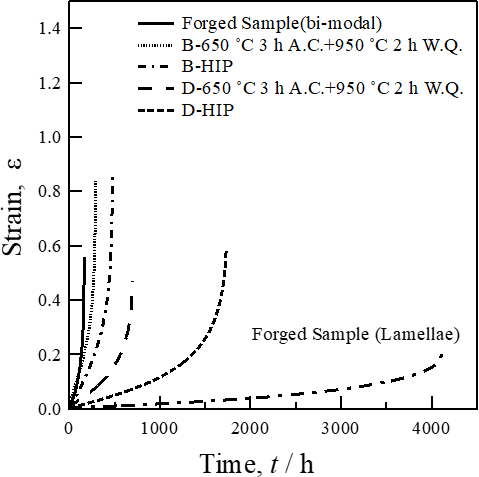
Creep curves recorded at 600 ℃ and 137 MPa for the SLM and forged samples. Creep life is governed by the grain size. A reduction of the porosities by HIP improved the creep rupture life.