Metallurgical Abstracts on Light Metals and Alloys vol.56
Improvement in Bonding Strength by Applying Circumferential Sliding in Cold Copper/Aluminum Forge-Bonding
Ryo Matsumoto*, Kakeru Hashimoto* and Hiroshi Utsunomiya*
*Division of Materials and Manufacturing Science, Osaka University
[Published in Journal of Materials Processing Technology, Vol. 307 (2022), 117685]
https://doi.org/10.1016/j.jmatprotec.2022.117685
E-mail: ryo[at]mat.eng.osaka-u.ac.jp
Key Words: Joining, Forging, Extrusion, Circumferential sliding, Dissimilar materials
To improve bonding characteristics of two dissimilar workpieces in cold forge-bonding, a processing parameter of circumferential sliding with respect to the forging axis on the contact interface was considered. In this forge-bonding process, stacked cylindrical workpieces of copper (upper) and aluminum (lower) were simultaneously backward-extruded into a cup shape between upper and lower punches. The upper punch was moved down along the forging axis, while the lower punch was rotated with respect to the forging axis. Forging speed was 0.1 mm/s, while circumferential sliding was applied by the lower punch with a rotation speed of maximum 1.5 rpm and a rotation angle of maximum 590° on the contact interface. Circumferential sliding did not change the geometrical profile and surface expansion of the contact interface, while it promoted bonding of aluminum on copper. As a result, the workpieces were bonded with approximately 25% shorter in the forging stroke and four times higher in the bonding strength at the same forging stroke. The maximum nominal bonding strength was approximately 30 MPa under a punch rotation angle of 590°.
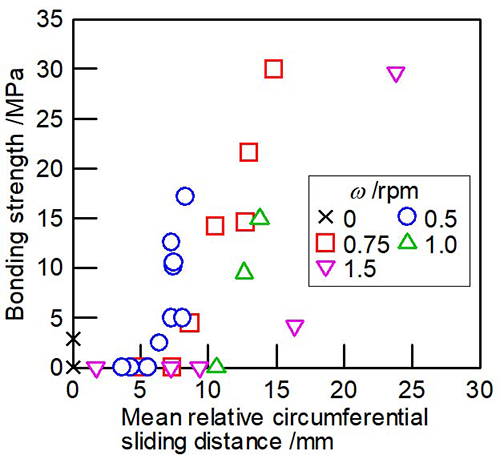