Metallurgical Abstracts on Light Metals and Alloys vol.55
Friction Stir Powder Incremental Forming for Fabrication of Sandwich-Structured Composite of Open-Cell Nickel Foam with Aluminum
Ryo Matsumoto*, Harutaka Sakaguchi*, Masaaki Otsu** and Hiroshi Utsunomiya*
*Division of Materials and Manufacturing Science, Osaka University
**Department of Mechanical Engineering, University of Fukui
[Published in Defect and Diffusion Forum, Vol. 414 (2022), pp. 179–184]
https://doi.org/10.4028/p-y07tfb
E-mail: ryo[at]mat.eng.osaka-u.ac.jp
Key Words: Friction stir process, Incremental forming, Porous metal, Skin surface layer
To fabricate sandwich-structure composite of porous metal with nonporous surface layer, the nonporous skin layer was formed on surface of open-cell type nickel foam from aluminum powder by friction stir powder incremental forming (FSPIF) process. In this process, the surface pores of the foam were filled with the powder, then the powder and the cellular matrix near the surface of the foam were incrementally hammered by a rod-shaped tool without rotation. After that, the hammered surface of the foam was incrementally stirred by the tool at a very high rotation rate. The formed skin layer was composed of two layers; the friction stirred layer (relative density: above 0.90) in the upper part and the compact layer (relative density: 0.60–0.90) in the lower part. The friction stirred layer with a maximum thickness of 0.8 mm was formed on the surface of the foam without deforming the cellular matrix of the inside of the foam under the forming conditions; a tool rotation rate of 8000 rpm, a tool feed rate of 60 mm/min, a tool pushing pitch of 0.1 mm, and a total forming depth of 5.0 mm.
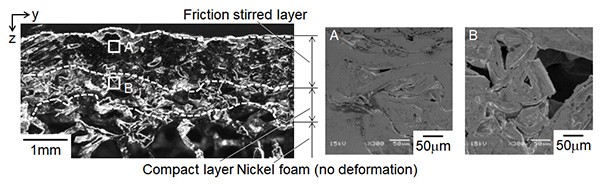